現代の日本では、コンピュータ科学の発展により、さまざまなデータが世の中を飛び交うようになってきました。そんな中、「ビッグデータ」という言葉を耳にしたことはないでしょうか。本記事ではまず初めに、ビッグデータとは何なのかについてご紹介いたします。
ビッグデータとは?
ビッグデータという言葉のみを聞くと、大量のデータのことをイメージする人は多いのではないでしょうか。この認識はあながち間違えではありません。しかし、ビッグデータというものはもう少し厳密に定義されています。
現在では、ビッグデータを構成する要素をまとめた「3V」というものがあり、Volume(データの量が多い)、Variety(データの種類が多い)、Velocity(データの生成頻度が高く、そのスピードが速いこと)の三つを満たすようなデータの塊をビッグデータと呼んだりしています。
今回は、データ収集の動向やメリットについてお話しするのですが、このビッグデータはデータ収集を語るうえで外せない知識であり、現在多くの企業がこのビッグデータを活用したシステムを利用しています。やはり収集するならビッグデータのような大きなデータのほうが有用性がありそうですよね。
製造現場(工場)におけるデータ収集の動向
では、どのようにしてビッグデータのようなデータを収集していくのかを簡単に確認していきましょう。
データ収集の動向を紹介するのですが、実は最近ではデータが至る所に存在しています。何かデータを探す特別な技術を持っていなくても簡単にデータを入手できてしまうのです。しかしながら、インターネット上にあふれているデータをそのまま使って解析を行おうとしても恐らく失敗します。なぜなら、インターネット上にあるデータには解析を行う上での不備があるからです。
解析を行う上での不備とは、エラーやノイズ、欠損値のことです。インターネットで見つけたデータはこれらが取り除かれていないことが多く、これを解析前に取り除いてから処理を行う必要があります。この取り除く処理を具体的に見ていきましょう。
まず、インターネット上で拾ってきたデータに対して、「データクレンジング」を行います。データクレンジングとは、データに含まれているエラーやノイズ、欠損値などを取り除く処理で、データを整えることで解析をしやすくします。データクレンジングの制度によってデータ解析に与える影響が大きいことから、この処理はデータ解析を行う上で最も重要とされています。
データクレンジングが終了したら、次にデータの統合を行います。ほとんどのデータがいろいろなソースから収集されているので、一貫性がありません。なので、これらのデータを整えるためにデータ統合を行う必要があります。
そして最後に、データを指定のフォーマットへ変換していきます。これでデータ解析のための前処理は終了です。
こういった前処理は非常に面倒なのですが、これらを怠ってしまうと適切な結果が得られず、せっかく行ったデータ解析が無駄になってしまいます。また、結果に多少の誤差を含むだけでなく、全く別の結果を出力してしまい、ビジネスに大きな影響を与える可能性があるため、十分に前処理は行っておく必要があります。
製造現場(工場)におけるデータ収集のメリット
ここでは、データ収集を企業が行う際のメリットについて考えていきましょう。現在、多くの企業がデータ収集を活用しており、その使用率は、大企業で9割、中小企業でも半数以上に昇ります。そんな多くの企業に必要とされているデータ収集ですが、近年では多くの企業が効率的なデータ収集を行うために「見える化」を行おうとしています。では、その「見える化」の例を少し見ていきましょう。
実際に、データ収集は企業にとって多くの利益を生み出すのですが、データ収集には多くの工数と時間が必要となります。それを解決するのが、IoTによる施設稼働実績監視システムです。これは一種の「見える化」といえます。
具体的には、IoTを活用することにより、リアルタイムでデータを収集し、人間がその状況をみえるようにします。これによりエラーが起きたタイミングや現在の作業量などを少数の人間が把握できるようになります。そうすることで、工数や人員も削減できるため、データ収集をより容易に行うことが出来るのです。
従来のデータ収集方法では、設備稼働記録のために人員・時間が必要だったり、各設備の記録をまとめる人間が必要だったり、人による記録が行われていたので正確性にも不安があったりしたのですが、IoTを用いた「見える化」を行うことでこれらの課題をまとめて解決することが出来ます。
それでは、以下で実際に「見える化」が成功した例をご紹介します。
機械の稼働率25%向上
こちらは、三友製作所における事例で、3種製品の製造を行うといったものであった。会社の課題としては、まずいくつかの向上で製造作業を行っていたため、生産管理者が電話で業務の割り振りを行わなければならないといったことがありました。また、生産管理システムを導入したのですが、現場の新たな改善への取り組みにはつながらないといった課題もありました。
このような課題を解決するために、本会社は工場に設置されている生産設備をネットに接続して、稼働状況を監視したり、蓄積したデータを分析して、加工計画の作成や予実比較を行ったりしました。
その結果、モニター上での稼働状況がわかり、業務振り分けがスムーズになったのです。それ以外にも、長時間機械が稼働していないという状態を把握して、原因解明を行い改善したところ、なんと稼働率を25%上げるといった結果になりました。
成形品の生産量を1.5倍
こちらは、株式会社土屋合成での事例で、この企業はボールペン等文房具や自動車製品などの製造の受託を行っていました。しかし、365日24時間体制ということもあり、夜間休日などは多くの人員が確保できずにトラブル等が発生してしまうといった課題を抱えていました。
そんな中、本会社は、成形機全49台の稼働状況のデータを取得して、管理者用PCよりすべての成形機の稼働状況を把握できる仕組みを構築しました。さらに、40台以上のカメラを設置して、工場のどこにいてもトラブルが発生した様子を閲覧できる仕組みを構築したのです。
これにより、夜間や休日の人員が少ない時間帯でも、トラブルの把握が容易になり、従来と同じ人員でより多くの成形機を稼働させることが出来るようになって生産量を1.5倍に向上させることに成功しました。
製造現場(工場)におけるデータ収集の課題
先ほど、工場で効率的にデータ収集を行うためにはIoTを導入する必要があるという風に述べたのですが、実は工場のIoT化にはある壁があります。それが、「OTデータの収集」です。工場でIoT化を進めるためには、各工場からのOTデータを収集しなくてはなりません。このOTデータの収集が課題となっているのです。
ERPなどのシステムが取り扱っているITデータは比較的簡単に集めることができ、データのフォーマットも一定の形に整っていることが多いです。これに対して、工場の装置・設備等からOTデータを収集するのはかなり難しく、データのフォーマットも統一されていないことが多いです。こうした事態は、今までITデータとOTデータが隔離されてきたからだといえるでしょう。
では、なぜOTデータのほうが集めるのが困難なのでしょうか。その理由は、データ散財にあります。工場の各種OTデータを集めようとしても、各工場が離れた位置にある場合は、インターネット経由で集めなくてはならないため、セキュリティの問題が生じます。また、OTデータは統一されていないので、そのままではIoTに活用することはできないのです。
まとめ
ここまで、工場におけるデータ収集の動向やメリット、課題についてご紹介してきましたが、データ収集についての理解は深まったでしょうか。データ収集はこれから先の技術を発展させるためにも、必須だといえるでしょう。このようなデータ収集を効率化するIoT化が有用なことは言うまでもありません。
しかし、工場におけるIoT化にはいまだ課題があることも事実です。このような課題を解決することにより、私たちの身の回りにあるシステムはさらに便利なものになるでしょう。
この記事の執筆・監修者
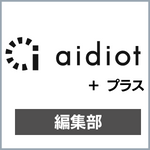
「BtoB領域の脳と心臓になる」をビジョンに、データを活用したアルゴリズムやソフトウェアの提供を行う株式会社アイディオットの編集部。AI・データを扱うエンジニアや日本を代表する大手企業担当者をカウンターパートにするビジネスサイドのスタッフが記事を執筆・監修。近年、活用が進んでいるAIやDX、カーボンニュートラルなどのトピックを分かりやすく解説します。